INTRODUCTION
Overuse of resources has increased greenhouse gas (GHG) emissions, causing serious environmental consequences such as climate change and global warming. The United Nations Food and Agricultural Organization (FAO) published its “Livestock’s Long Shadow” report in 2006, which illustrated the wide-ranging environmental impact of livestock production [1]. According to this assessment, animal products, such as red meat, dairy, and eggs, account for 18% of worldwide GHG emissions, more than industry (16%), transportation (13.5%), and energy usage (13%). The Chair of the Intergovernmental Panel on Climate Change (IPCC) warned about environment burden of meatproduction and consumtion on a presentation titled “Global Warning - The Impact of Meat Production and Consumption on Climate Change.”[2]. Livestock accounts for 80% of the global agriculture sector [1], produces 30% of the world’s protein consumption, plays a key nutritional function in delivering necessary amino acids, alleviates poverty for around one billion people, and has social significance in providing jobs for over one billion people [1,3].
Life cycle assessments (LCAs) for animal products and livestock areas have been conducted in the United States, Canada, Australia, New Zealand, and Europe [4]. Furthermore, research on meat production and consumption has been conducted in Japan, based on animal farming conditions that are similar to those in South Korea [5,6]. According to these studies, the carbon footprint of beef production ranges from 9.9 to 34 kg CO2 equated (CO2-eq)/1 kg carcass (grain-fed in Australia and feedlot in Japan) Carbon emissions were found to depend on feeding and management conditions (see Table 1 [7-12]). Japan’s feedlot system emits 34.3 kg carbon dioxide (CO2)-eq, making it the country with the highest carbon emissions from beef production. Carbon emissions from pork production ranges from 2.3 to 6.42 kg CO2-eq/1 kg of dead weight (French and UK) (see Table 2 [13-18]), with carbon emissions depending on feeding and management conditions [14-19].
Country (system) | GHG emissions (kg CO2-eq) | Functional unit | References |
---|---|---|---|
Japan (feedlot) | 34.3 | kg beef | [7] |
USA (feedlot) | 14.8 | kg live weigh | [8] |
USA (backgrounding/feedlot) | 16.2 | kg live weigh | [8] |
USA (pasture) | 19.2 | kg live weigh | [8] |
Australia (grain-fed) | 9.9 | kg HSCW | [9] |
Australia (grass-fed) | 12 | kg HSCW | [9] |
Sweden (organic) | 22.3 | kg bone free meat | [10] |
EU steer (over 24 months) | 19 | kg meat | [11] |
Canada (feedlot) | 22 | kg of beef | [12] |
South Korea (feedlot) | 16.55 | kg of live weight | Current study |
South Korea (feedlot) | 27.87 | kg trimmed beef | Current study |
Country (system) | GHG emissions (kg CO2-eq) | Functional unit | References |
---|---|---|---|
France (good agricultural practice) | 2.3 | kg live weight | [13] |
UK (heavier finishing) | 6.08 | kg pig meat | [14] |
UK (indoor breeding) | 6.42 | kg pig meat | [14] |
UK (outdoor breeding) | 6.33 | kg pig meat | [14] |
UK (non-organic) | 6.36 | kg pig meat | [14] |
Netherlands (conventional) | 3.7 | kg live weight | [15] |
Denmark | 2.25 | kg live weight | [16] |
Canada | 2.31 | kg live market weight | [17] |
Australia (crop/feed production) | 3.1 | kg HSCW | [18] |
South Korea (feedlot) | 2.62 | kg live weight | Current study |
South Korea (feedlot) | 12.3 | kg trimmed meat | Current study |
As Tables 1 and 2, LCAs of different animal products have been conducted by cattle-power nations such as the United States, Canada, Australia, New Zealand, and many countries in Europe. United States have looked specifically at carbon emissions at the farm gate (from the cradle to the farm), after the farm gate (packing, storage, retail), during the distribution process, and during cooking [20]. Japan, industrial context is similar to that of South Korea in terms of imported animal feed supplies and beef marbling, has been conducting LCAs of meat and meat products since the early 2000s.
Since 2012, the Korean government has approved 51 “low-carbon agricultural products,” with 19 using low-carbon or zero-carbon technologies. However, low-carbon products from animal resources have not been developed or certified so far. In the current study, we therefore estimated amounts of carbon emissions during the production and distribution of beef and pork in the South Korean animal industry. This study represents the first attempt at estimating CO2 emissions from animal products, and we based it on a selection of exemplar cases of industrial farms and slaughterhouses. In addition, we also estimated CO2 emissions from imported beef from selected countries.
MATERIALS AND METHODS
The Publicly Available Specification (PAS) 2050:2011 (UK guidelines) and educational data from the Korea Environmental Industry & Technology Institute (KEITI; A course for life cycle evaluation theory and practice) were used to establish the methodology for calculating GHG emissions in the domestic beef and pork production and distribution process. To assess GHG emissions, the meat production and distribution system (Fig. 1) was divided into different stages: production, slaughter, distribution, and import. During the manufacturing process, all GHG emissions were transformed into the equivalent amounts of CO2.
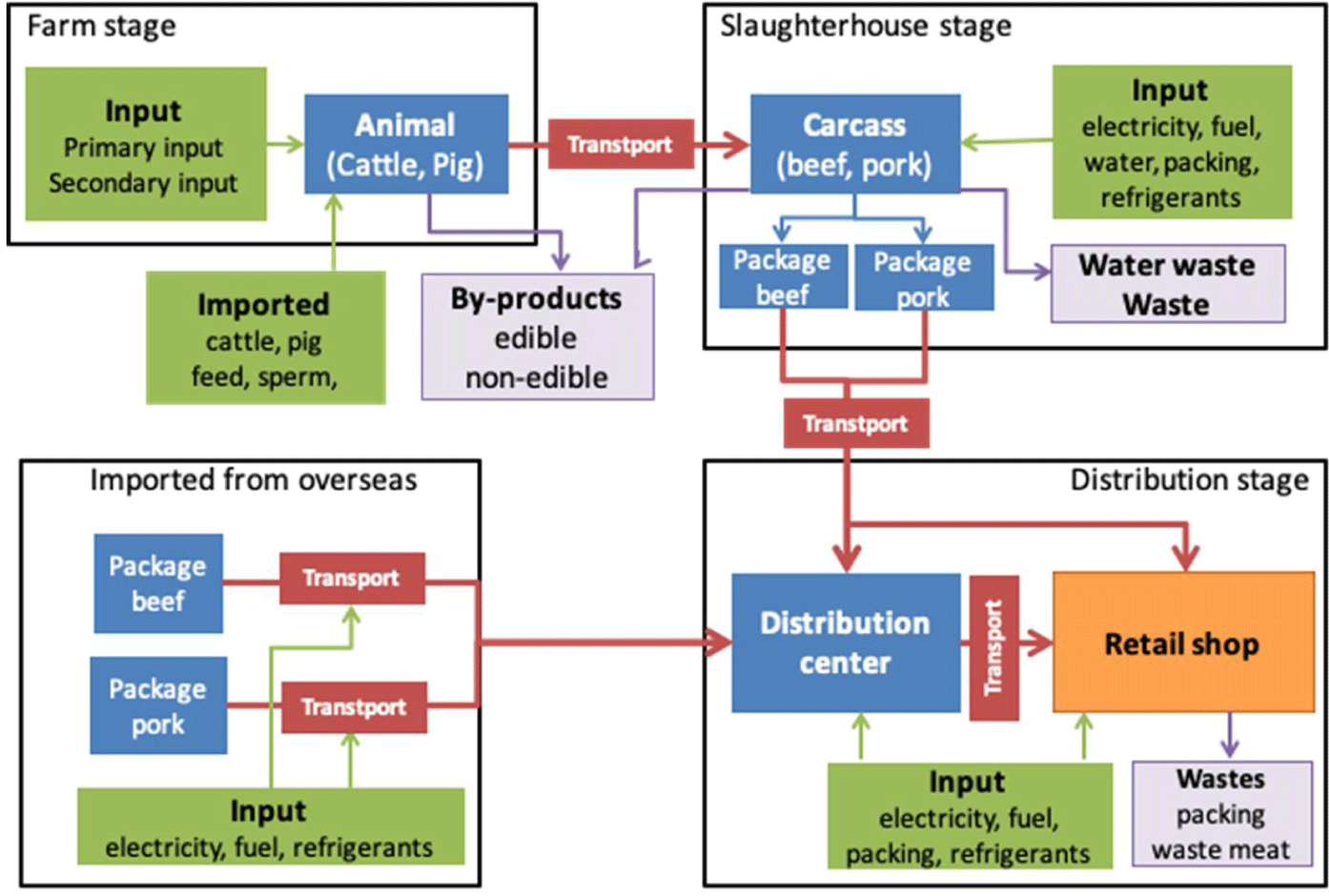
Using case examples, GHG emissions were calculated at the farm level and at the slaughterhouse level. System boundaries were determined at the farm stage to explore the input and output of all materials, resources, and waste on cattle-producing farms. A typical Hanwoo steer farm’s system boundary is depicted in Fig. 2. The system begins with the intake of a 6-months-old calf, and after for about 24 months of feeding, the animal is ready for shipping, the animal designated as “Product #1”. A typical pig farm’s system boundary is depicted in Fig. 3. “suckling pigs” that was born from a gilt in a farm, which then go through the life cycle, from “weaning pigs” to “piglets” and then “growing pigs”, who are eventually shipped (Product #1). Another option to produce at a pig farm stage is to sell the piglets after weaning (see “Product #2” on Fig. 3). Fig. 4 depicts the system boundaries of a slaughterhouse, where two types of processes take place. Cattle and pigs are slaughtered in “Unit process #1”, non-consumable waste is removed immediately, cool down for regular times in cold chamber, and finally remains are cold carcasses. Slaughterhouses hold auctions for some part of the cold carcasses processed “Unit process #1”, and some goes to a processing plant in the system boundary of a slaughterhouse (Unit process #2). The deboning and packaging of cold carcasses of both pigs and cattle follows in “Unit process #2”. The end products of this process are primal beef and pork cuts ready for shipping.
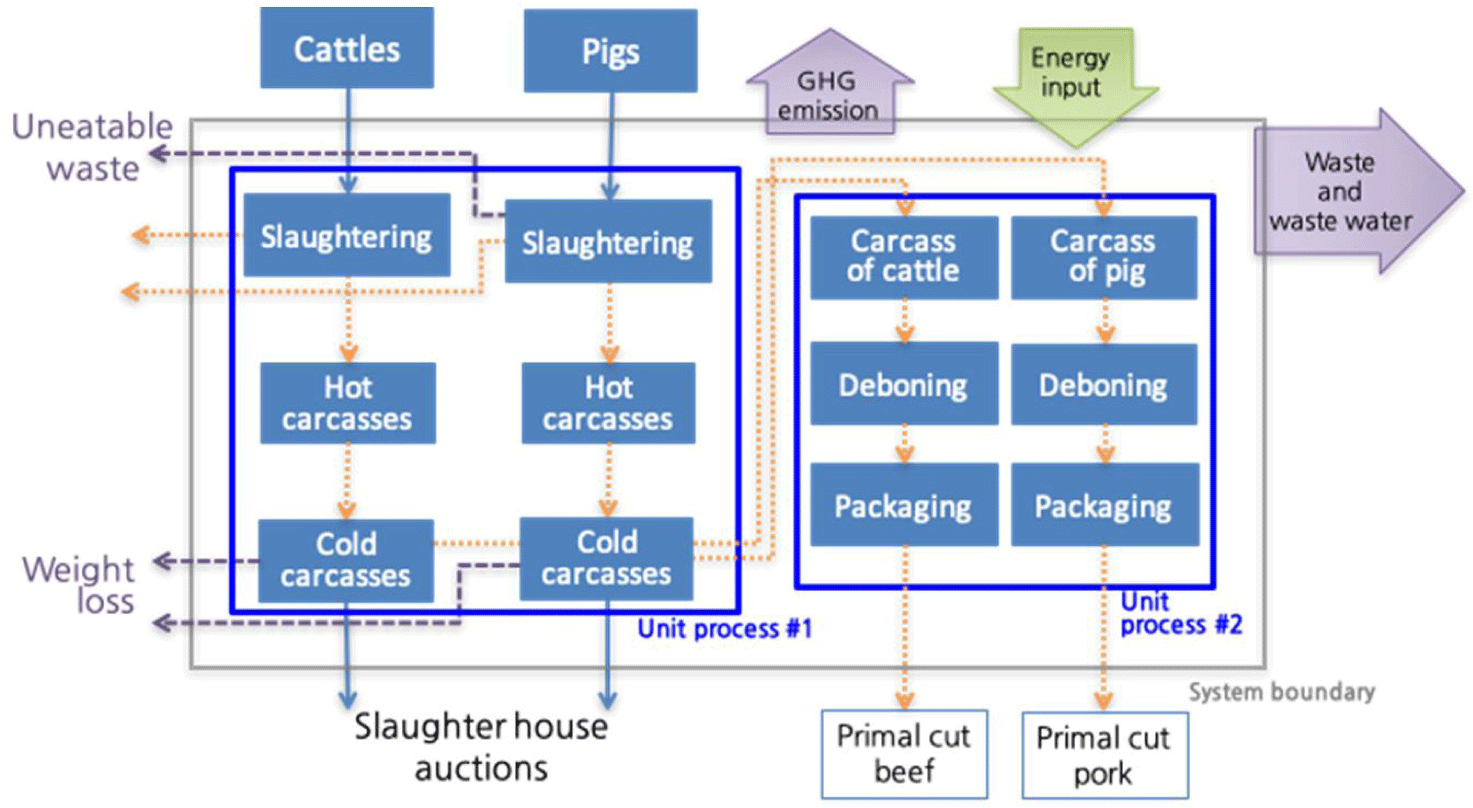
Data was collected based on the system boundaries of each stage for our computation of GHG emissions, entered into a record table once the process chart was created, and all obtained data were checked once more before the analyses. The unit process was determined based on the company’s management data, and a process flow chart was constructed by connecting the two units. One cattle production farm (located in Jeongeup, Jeollabuk-do) and one domestic pig farm (located in Wanju, Jeollabuk-do), one slaughterhouse in Iksan, Jeollabuk-do, and one slaughterhouse in Bucheon, Gyeonggi-do were targeted for the evaluation of the farm and slaughterhouse stages during the beef and pork production process.
The farm used for our analysis was a typical Hanwoo rearing farm, where calves were grown, fattened, and then sent for slaughter. The calves were about 6 months old when they were taken in, and grown and fattened for roughly 24 months. After fattening, the cattle (about 30 months old at that point) were transported to a slaughterhouse. The amount of GHG emissions at the cattle farm stage was determined using a unit material of 1 kg of live weight of cattle moved from the farm. The influence of feed transport and equipment was not factored into our calculation of GHG emissions at cattle farms.
The pig farm targeted for the current study was a typical enclosed house with gilts and sires, and some of the piglets born on the farm were sold to people outside of the farm. Other piglets that stayed inside this farm’s boundaries were shipped to a slaughterhouse after finishing (finishing pigs) or sold to another pig farm after growing (selling sows). Shipping pigs (for meat production; “product #1” in Fig. 3), selling pigs (weaned piglets; about 8.5 kg per head; “product #2” in Fig. 3), piglets (approx. 17 kg per head; “product #2” in Fig. 3), and sows were among the pig farm’s output products. As unit material, 1 kg of live weight of finishing pigs sent from the farm was used to estimate GHG emissions during the pig farm stage. Additionally, GHG emissions from selling pigs at the farm stage were estimated using the weight of each selling pig (weaning piglets and piglets). The influence of feed transport and equipment was not factored into our calculation of GHG emissions at pig farms.
Two domestic slaughterhouses were used as case examples to assess the quantity of GHG emissions during the process of killing cattle and pigs and the production of primary meat. Both slaughterhouses have each slaughtering process line for cattle and pigs on the same plant, and in addition to the slaughter area, they also comprise primary processing facilities (for deboning, trimming, and packaging). We collected all data of slaughter unit and meat primary process unit at one slaughterhouse (A), and only gathered data of slaughter process at the other slaughterhouse (B) due to limitation of meat primary process unit data collecting. GHG emissions during the slaughter process were estimated for 1 kg of hot carcasses of cattle/pig. Moreover, using 1 kg of chilled beef and/or pig as a functional unit, we also calculated GHG emissions from basic meat processing operations.
CO2-eq emissions at the farm and slaughterhouse stages were computed using databases from the KEITI [21], the Food Ecoinvent (Switzerland), and the Simapro (Denmark). The results derived from the farm stage were used to create a GHG emission database of live animals. Table 3 [7,21-24], based on reference literature [7,22-24], lists the quantity of GHG emissions generated during the meat distribution process as well as the energy consumed during retail storage.
Amount of CO2-eq emissions (unit) | References | |
---|---|---|
CO2-eq from packaging and ageing | ||
Packaging | 0.6 (kg CO2/kg meat) | [7] |
Ageing period (0°C–2°C)1) | 0.7 (kg CO2/kg meat) | [7] |
CO2-eq from energy use for cold storage | ||
Industrial storage | 0.00015 (kWh/kg/day) | [22] |
Supermarket storage | 0.0009 (kWh/kg/day) | [23] |
Supermarket display | 0.044 (kWh/kg/day) | [23] |
Household storage | 0.0054 (kWh/kg/day) | [24] |
CO2-eq from transport and electricity use | ||
Marine transport (ship, container carrier) | 0.0092 (kg CO2/ton per km) | [21] |
Road transport (truck) | 0.249 (kg CO2/ton per km) | [21] |
Electricity use | 0.495 (kg CO2/KWh) | [21] |
We used the PAS 2050:2011 (UK) and the KEITI guidelines of educational materials (A course of live cycle evaluation theory and practice). Data (excluding energy and transportation) were derived from international databases, because there is currently no database related to the agricultural and livestock industry in South Korea that quantifies CO2-eq emissions. Agricultural data were found in the Ecoinvent (Switzerland) and Simapro (Denmark) databases, as presented in Table 4 [6,21,25-27]. Because there are no databases that provide information on the different types of GHG emission for input feed production, we combined the most similar types of data and excluded. Dry matter intake (DMI, kg/day) was used to compute intestinal fermented gas emissions, based on the following formula [28]:
Database list | CO2-eq emissions | Unit | References |
---|---|---|---|
Animal feed | |||
Grain maize | 5.99E-08 | kg CO2/kg | [25] |
Soybean meal | 2.62E-08 | kg CO2/kg | [26] |
Grass | 3.41E-08 | kg CO2/kg | [25] |
Cornflake | 5.00E-08 | kg CO2/kg | [25] |
Domestic transport | |||
Road transport (truck) | 2.49E-01 | kg CO2/ton per km | [21] |
International transport | |||
Container ship (average) | 1.35E-02 | kg CO2/ton per km | [21] |
Energy and water use | |||
Electricity | 4.95E-01 | kg CO2/kWh | [21] |
Diesel | 6.82E-02 | kg CO2/kg | [21] |
Kerosene | 2.53E-01 | kg CO2/kg | [21] |
LNG | 5.95E-01 | kg CO2/kg | [21] |
LPG | 3.94E-01 | kg CO2/kg | [21] |
Fuel combustion | |||
Diesel | 2.60 | kg CO2/kg | [21] |
Kerosene | 2.45 | kg CO2/kg | [21] |
LNG | 2.78 | kg CO2/kg | [21] |
LPG | 3.64 | kg CO2/kg | [21] |
Water | 3.32E-04 | kg CO2/kg | [21] |
Waste treatment | |||
Slurry store and processing | 5.81E-05 | kg CO2/m3 | [25] |
Disposal of bone, blood and waste meat | 2.61E-08 | kg CO2/kg | [26] |
Wastewater treatment | 1.28E-03 | kg CO2/kg | [21] |
Waste landfill | 3.99E-02 | kg CO2/kg | [21] |
Waste incineration | 1.23E-01 | kg CO2/kg | [21] |
Others | |||
Refrigerants (CHCIF2) | 1.81 | kg CO2/kg | [6] |
CH4 | 25 | kg CO2/kg | [6] |
Calf over 8 months | 19.2 | Kg CO2/head | [27] |
The amount of nitrogen generated from manure was calculated using crude protein (CP), total digestible nutrients (TDN), and dry matter (DM) of the feed, based on the following formula [29]:
GHG emissions from meat storage were calculated considering only electricity use. The database [21] used to derive data on electricity use for storage is depicted in Table 3.
GHG emissions from marine transportation during the import–customs–clearance–distribution phase of beef and pork import were computed as CO2-eq emissions. The mode of transit was considered to be a container ship, the calculation excluded effects from refrigerants (for freezing or refrigeration), packaging materials, storage temperatures. The Ministry of Environment of Korea’s Life Cycle Inventory Database (LCI DB) was utilized to calculate as CO2-eq emissions of container ships for transit (Table 4). In addition, using the Korea Hydrographic and Oceanographic Agency’s database, the distance between export ports of each country and Incheon Port in South Korea was estimated. Data on quarantined imported livestock products from the Korea Meat Trade Association (KMTA) were used to estimate the amount of imported meat for one year (2011.4.–2012.3.) [30]. As for beef, the United States, Australia, New Zealand, Canada, and Mexico imported a total of 275,719 tons. Since the United States, Australia, and New Zealand account for 98% of beef imports, only date from these countries were used to calculate GHG emissions. During the same period, a total of 383,348 tons of pork were imported from the United States, Canada, Chile, the Netherlands, Austria, France, Denmark, Belgium, Poland, Hungary, and other countries. For the estimate of GHG emissions from imported pork, we included data from the United States, Canada, Chile, the Netherlands, Austria, France, Denmark, Belgium, Poland, and Hungary. While imported beef is transported to South Korea by sea and air, we estimated GHG emissions under the assumption that all the products were transported by the container carrier vessel. Additionally, neither the time spent traveling from the production site to the port for marine transportation nor the time spent waiting for customs clearance and quarantine after arriving at the domestic port were included in our analysis.
RESULTS AND DISCUSSION
A Hanwoo farm’s system boundary is shown in Fig. 2, using a 6-month-old calf that was raised for roughly 24 months before being delivered to a slaughterhouse as an example. 1 kg of live Hanwoo steer emitted a total 16.551 kg CO2-eq (Table 5), it was shown lower than other countries (see Table 1). We presumably be attributed because limit of our analysis that we did not take feed transportation and mechanical equipment into account. In case of Japan, which has a comparable feeding environment and system, only a small amount of CO2-eq was generated by equipment and by feed production and transportation accounted for 40% of total CO2-eq generation [5]. We therefore expected higher GHG emissions from Hanwoo beef production than our analysis determined. South Korean red meat production is based on feedlots and heavily reliant on imported grain, which is used to feed high TDN diets to cattle. Furthermore, because the South Korean beef market requires substantial intramuscular fat, long-term fattening follows breeding for more than 30 months on average. Because the Korean beef production system includes such a long fattening period, we believed that the environmental impact of beef production and consumption would be greater than what has been reported in other major agricultural countries. The global warming potential (GWP100) of methane, a primary GHG produced during digestion, was 25, making it the most significant source of CO2 produced during beef production. The amount of methane gas generated per day by a Hanwoo steer in our sample was 301 L, and when translated to kg using the methane weight conversion factor (655.6 µg mL−1), 0.1975 kg of methane gas was generated. At the farm we selected, a steer released 144.7 kg of methane over the course of 24 months, from calf adoption to shipment. To put it another way, a steer produced 72.35 kg of methane each year (Table 5). The amount of methane produced by digestion is determined by the amount of TDN present in the animal’s diet [28,29]. The annual methane production per cow has been reported to be 53 kg in North America and 60 kg in Oceania, according to the IPCC. The relatively high methane output of the Hanwoo farm in the current study can presumably be attributed to the fact that it feeds animals a total mixed ration diet with a high TDN.
The pig farm we selected was a standard enclosed housing system, and its system boundary is depicted in Fig. 3. The GHG emissions of all pig farm products are presented in Table 6. The farm stage emitted a total of 2.621 kg of equated CO2 per 1 kg of live finishing pig weight. The GHG output of an 8.5-kg weaning piglet was estimated to be 22.015 kg CO2-eq, and that of a 17-kg piglet 45.603 kg CO2-eq. Other countries report CO2-eq emissions from generating 1 kg of live pig weight of 3.7 kg (Netherlands), 2.25 kg (Denmark), and 2.31 kg (Canada) (Table 2), similar to our findings. However, our analysis was limited by the fact that we did not consider feed transportation and processing as factors, due to the limited availability of data on the domestic pork production process, a direct comparison with data from other countries is therefore not possible. However, if a domestic GHG emissions inventory of feed processing is established that a more accurate comparison would be possible.
Two slaughterhouses were used as example cases to calculate the amount of GHG emitted during the process of slaughtering animals and primary meat processing. Table 7 shows that for 1 kg of hot carcass or edible byproducts, 0.107 kg and 0.065 kg CO2-eq were emitted from each slaughtering process at the slaughterhouse stage. From 1 kg of hot cattle carcass, 17.581 kg and 17.404 kg CO2-eq were emitted, 1 kg of hot pig carcass emitted 2.468kg and 2.944 kg CO2-eq, at slaughterhouses A and B. At the slaughterhouse A, 27.419 kg CO2-eq was emitted from1kg of trimmed beef, 1 kg of packaged beef emitted 27.866 kg CO2-eq, 1 kg of trimmed pork emitted 12.305 kg CO2-eq, and 1 kg of packaged pork emitted 12.753 kg CO2-eq. From 1 kg of hot pig carcass at slaughterhouse A emitted more about 0.5 kg of CO2-eq than slaughterhouse B. The gap of CO2-eq emissions from hot pig carcass was determined by the amount of edible and disposal byproducts created during the slaughterhouse process. This result shows possibility that GHG emission from meat can therefore be reduced by increasing the use ratio of edible and disposal byproducts. Furthermore, because most processes involved in the beef and pork trimming stage are conducted under 4°C, the amount of GHG produced by the use of refrigerants and power was significant. Additional GHG were produced during the packaging stage, where they emit from primary packaging materials such as plastic and wrapping materials for retail distribution as well as from secondary packaging materials such as paper and cardboard.
We also estimated the amount of GHG generated before the consumer buy the beef during the usual distribution process of domestic beef (see Table 8). The calculation just took into account electricity usage; refrigerants were left out because different refrigerants may lead to significant deviations. We found that 0.170 kg of CO2 -eq is emitted for 1 kg of beef for the maximum estimated time between slaughterhouse, processing factory, and the consumer’s table. In 2012, Korea’s annual per capita beef consumption was 9.7 kg and beef self-support was 4.2% [31], implying that one person is responsible for 0.795 kg CO2-eq of greenhouse emissions over the course of a year. In 2012, a total of 245,290 tons of beef were produced [32], and it was expected that electricity use caused a total of 41,699 kg CO2-eq GHG during the distribution period till the meat was eventually consumed. Despite the fact that the 2012 estimate of beef distribution-related GHG emissions was based on simple calculations, it points to the possibility of reducing emissions that might occur during the ripening or storage period.
For meat distribution, 0.0009 kWh/day of electrical power is needed to store 1 kg of chilled meat, while 0.044 kWh/day of electrical power is used to chill a 1-kg meat display in retail [23]. In general, the customs process and the quarantining of imported beef takes around 30 days in South Korea. If domestic beef was stored for the same amount of time (30 days), storage and display would produce 0.013 kg CO2-eq and 0.653 kg CO2-eq, respectively.
Table 9 illustrates the origins and quantities of beef imported into South Korea in the year prior to our study. Between April 2011 and March 2012, a total of 275,719 metric tons of beef were imported from the United States (107,025 metric tons), Australia (135,404 metric tons), New Zealand (29,517 metric tons), Mexico (3,752 metric tons), and Canada (3,752 metric tons) (CA; 21 ton). Of the total, 98.6% (271,946 tons) was imported from the United States, Australia, and New Zealand, which are located around 10,000 km away from South Korea by sea. From April 2011 to March 2012, the transport of beef imported on container vessels caused a total of 24,995 tons of CO2-eq emissions. In other words, importing 1 ton of beef causes 92.18 kg of CO2-eq emissions.
Determined using the “Korea Hydrographic and Oceanographic Agency” webpage, at https://www.khoa.go.kr/kcom/cnt/selectContentsPage.do?cntId=31307000.
Table 10 shows the origins and quantities of imported pork in 2011. A total of 383,348 tons of pork from the United States, Canada, Chile, the Netherlands, Austria, France, Denmark, Poland, and Hungary was shipped to South Korea. The marine distances of countries without a port were used as the distances between European countries. Our analysis shows that 1 ton of imported pork produced 108.62 kg CO2-eq on average, more than imported beef (91.91 kg CO2-eq). The difference in GHG emissions between imported pork and beef is due to the fact that beef is imported from countries at distances of around 10,000 km, such as those in the Americas and Oceania, whereas pork is largely imported from European countries, which are further away from South Korea. The sea transport of imported beef over the course of 1 year thus caused 25,416,205 kg of CO2-eq, while the transport of imported pork produced 41,637,954 kg of CO2-eq. These numbers suggest that replacing 50% of imported beef and pork with local beef and pork will reduce emissions by more than 30 million kg of CO2-eq per year. Garnett [33] asserted the greatest method to minimize GHG emissions is to follow nature’s lead. In line with that notion, our findings also show consuming local foods can reduce GHG emissions.
CONCLUSION
We found that total amounts of CO2-eq from the production of 1 kg live weight of cattle and pig in South Korea, 16.55 and 2.62 kg, are relatively low, while those for packaged beef and pork, 27.9 and 12.75 kg, are much higher. The stage that has the largest impact on the amount of CO2-eq generated in the production/processing of red meat (beef and pork) ready to be consumed is the livestock farm. This suggests that low-carbon technologies used in the enteric fermentation and manure waste sectors could effectively and greatly reduce carbon emissions at the farm stage. In addition, reconsidering the high-TDN diets fed to Hanwoo cattle could be a starting point to reduce methane emissions from beef production. CO2-eq emissions from pork production in South Korea are similar to those reported in other countries, but considering the limited data on feed that were available for this study, higher levels of emissions were expected. A database on feed production (including cattle feed) is needed to accurately calculate GHG emissions from pork and to find ways to reduce GHG during domestic pork production. Moreover, given that transportation of imported grains and other feed ingredients was not taken into account in the current study, emissions related to animal feeds can be increased and consequently elevates total amount of carbon emission for the animal products. This highlights the importance of domestic and local feed supplies for the reduction of carbon emissions from animal products. During the distribution and storage of red meat, reducing the storage period (especially the ripening period of beef) may help reduce GHG emissions; future studies should investigate this point further.
The data for the current study were obtained from example cases of selected farms with specific conditions, and our findings can therefore not necessarily be extended to Korean meat products in general. However, this study represents the first attempt at estimating CO2-eq emissions from animal products in South Korea and provides important insights for potential future initiatives to reduce emissions during the production and distribution of meat.